Home
zurück
Eigenbau eines Faltbootes - Seite 5
Direkt zu Seite... 1 / 2 / 3 / 4 / 5 / 6 / 7 / 8
zurück
Einige Bootsbauer verzichten in ihren Booten vollständig auf eine Bodenleiter und sitzen auf einem Stück Schaumstoff oder einem wasserdichten Kleidersack. Die Vorstellung, beim Einsteigen einfach so auf Kiel und Bodensenten und die Bootshaut zu treten, gefiel mir überhaupt nicht. Also habe ich eine Bodenleiter eingebaut.
Ursprünglich hatte ich auch einen recht ergonomischen Holzsitz auf der Bodenleiter befestigt. Jedoch war die Sitzposition zu niedrig, und so habe ich ihn (auch aus Platz- Gewichtsgründen) wieder ausgebaut. Mittlerweile sitze ich auf einem Faltsitz der Firma "Crazy Creek", den ich etwas modifiziert habe.
 Die Bodenleiter besteht aus zwei Vierkanthölzern, auf die ich Platten aus Alu-Verbundmaterial geschraubt habe. In der Mitte habe ich etwas Platz gelassen, so kann ich sehen, wieviel Wasser im Bereich des Kiels schwappt und komme dort auch mit der Handlenzpumpe gut heran. In den Vierkanthölzern stecken hinten jeweils ein Bolzen, die durch Bohrungen in Spant 3 gesteckt werden. Vorn in den Vierkanthölzern befinden sich M6-Einschlaggewinde aus Messing. Dort wird die Bodenleiter mit Flügelschrauben, die durch Bohrungen in Spant 2 gesteckt werden, gesichtert. Die Bodenleiter liegt direkt auf dem Kiel auf.
Vor dem Spant zwei liegt direkt auf dem Kiel die Fortsetzung der Bodenleiter. Sie wird ebenfalls mit 2 Stiften, die in Bohrungen im Spant 2 stecken, gesichert. Fixiert wird diese "halbe Bodenleiter", die nicht bis zum Spant eins reicht, mit zwei Winkeln, die links und rechts vom Kiel anliegen, und einem Splint mit Gummiband, der durch ein Loch im Kiel gesteckt wird.
Auf diesem vorderen Ende der Bodenleiter sind mit 2 Scharnieren 2 Pedale aus Alublech befestigt.
Damit ist das Bootsgerüst fertig.
Für das Lackieren sollte man sich unbedingt Zeit nehmen und lieber etwas zu sorgfältig arbeiten, als das man Kleinigkeiten vernachlässigt. Wasser kann in noch so kleine Ritzen eindringen und dort dafür sorgen, dass Sperrholz aufquillt, was unter Umständen irreparable Gerüstschäden nach sich ziehen kann.
Zum Lackieren empfehle ich Bootslack, ich selbst habe aus Kostengründen einfachen Buntlack verwendet, den ich noch vorrätig hatte ( ich habe während dieses Bauabschnittes das ganze Projekt immer noch als eine Art Experiment betrachtet ). Vor dem 1. Anstrich sollten alle Gerüstteile noch einmal mit feinem Sandpapier geschliffen werden. Winklige Kanten sollten mit einem kleinen Hobel mit einer Fase versehen, die verbliebenen Kanten rund geschliffen werden. Es hat sich gezeigt, dass an scharfen Ecken und Kanten der Lack bei Stößen viel schneller abplatzt als an solchen Stellen, die abgerundet waren. Bohrungen in den Gerüstteilen sollten ebenfall mit Schleifpapier nachgearbeitet werden, insbesondere die Ränder der Löcher. Anschließend entfernt man sorgfältig Schleifstaub und Verschmutzungen.
 Als erstes sollte man die Flächen zwischen den einzelnen verschraubten Bauteilen lackieren, sofern diese nicht mit Holzleim zusammengefügt wurden. Dazu löst man die Schrauben, bringt mit einem kleinen Pinsel zwischen den Teilen etwas Lack auf und zieht die Schrauben anschließend wieder an. Der trocknende Lack verklebt die Bauteile zusätzlich, es kann kein Wasser eindringen, die Stabilität wird erhöht. Aus den Fugen quellender Lack solle mit einem Lappen entfernt werden.
Dann folgt der 1. flächige Anstrich aller Bauteile. Dazu solle man den Lack mit Verdünnung hochflüssig verdünnen. Dieser wasserartige Lack dringt leicht in kleine Fugen ein und wird vom Holz gut aufgesogen. Es sollte aber unbedingt vermieden werden, Tropfnasen entstehen zu lassen. Übrigens empfieht es sich, etwas bessere Pinsel zu nehmen, die nicht ständig Haare verlieren. Wer hat, kann auch mit einer Spritzpistole lackieren.
Nach dem Trocknen fühlt sich die Oberfläche der Bauteile sehr rauh an. Ursache dafür ist, dass die Holzfasern den Lack aufgesogen haben und aufgequollen sind. Alle Bauteile müssen daher anschließend mit feinem Schmirgelpapier geglättet werden, der Schleifstaub wird mit einem weichen Tuch abgewischt. Anschließend erfolgt der zweite Anstrich, der nun mit nicht ganz so stark verdünntem Lack erfolgen sollte.
Nach dem 2. Lackieren wird wiederholt geschliffen und anschließend das 3. mal lackiert, diesmal mit unverdünntem Lack. Anschließend sollte man die Gerüstteile gut durchtrocknen lassen, bevor man sich an die nächsten Arbeitsschritte wagt. Damit ist der Gerüstbau abgeschlossen.
Ich habe es mir damals nicht nehmen lassen, eine erste Testfahrt mit dem Boot zu unternehmen. Ich habe also das Gerüst aufgebaut und anschließend in eine 5 Meter lange transparente Baufolie eingeschlagen, die ich mit Klebeband etwas gestrafft hatte. Anschließend habe ich das gesamte Boot mit Frischhaltefolie eingewickelt und mit einem scharfen Messer die Luke wieder geöffnet. Anschließend ging es ab an einen kleinen Fischteich bei mir in der Nähe.
|
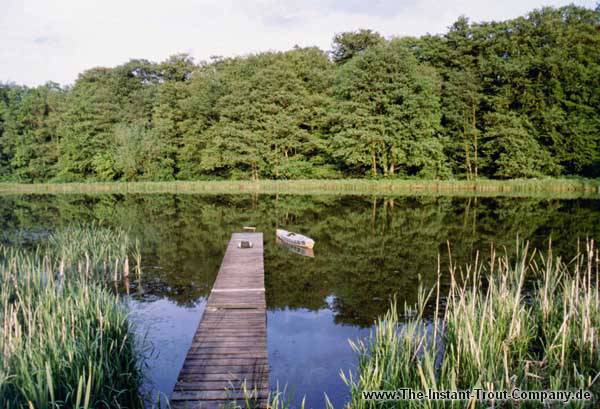
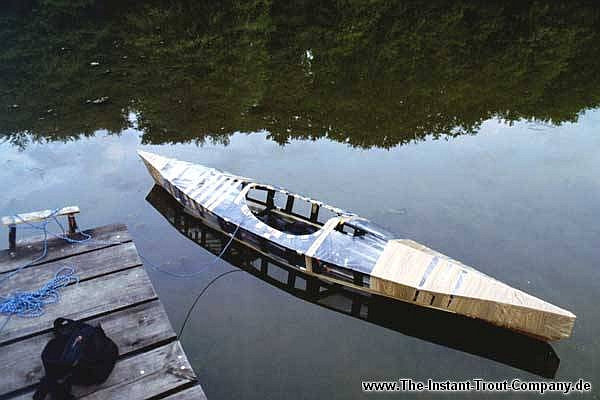
Auf den ersten Metern war ich noch etwas skeptisch, ob die Folie halten würde. Dann aber bin ich beherzt darauf los gepaddelt. Diese Testfahrt diente vor allem dazu, herauszufinden, ob das Boot konstruktive Mängel aufwies. So bemerkte ich schnell, dass das Boot, wenn man es treiben ließ, nicht geradeaus lief, sondern nach links oder rechts wegdriftete. Ein Lenken durch Ankanten des Boote hat nicht geklappt, was aber mehr auf meine mangelnden Fähigkeiten als Paddler zurückzuführen ist. Ein Festsaugen des Hecks bei höheren Geschwindigkeiten hab ich nicht feststellen können. Letztendlich habe ich keine Änderungen mehr am Gerüst vorgenommen.
Die Haut - einige Vorbemerkungen |
Zu Beginn der Faltbootära Anfang des 20. Jahrhunderts bestanden die Bootshäute meist aus sehr dichtgewebter Baumwolle, die im Bereich des Unterschiffes mit mehreren Schichten aus Naturkautschuk wasserdicht gemacht wurden. Etwa seit den 50er Jahre Jahren wird vermehrt ein Kunstfaser-Trägergewebe verwendet, das entweder mit PVC oder mit Hypalon, einem Produkt aus dem Hause Du Pont, beschichtet ist. PVC kann geschweißt und gelebt werden, Hypalon wird vulkanisiert. Hypalon soll etwas widerstandsfähiger sein, während PVC langsamer altert. Die Lebensdauer einer Bootshaut liegt je nach Pflege wohl bei etwa 30 Jahren. Hypalon sollte zudem gelegentlich mit einer speziellen Pflegeemulsion behandelt werden, die ein Verhärten verhindert.
Vor der Anfertigung der Haut habe ich recht intensiv diverse Internet-Seiten und Foren durchstöbert, um herauszufinden, welche Art von Bootshaut sich am leichtesten realisieren ließe. Verschiedene Ideen geisterten durch meinen Kopf. Hypalon schied relativ früh aus, da es in Kleinmengen wohl recht schwer zu bekommen ist. Eine Überlegung war, eine Haut aus Cordura, einem sehr reißfesten Nylongewebe aus dem Hause Du Pont, zu nähen und anschließend selbst zu beschichten. Hierzu verwenden einige Bootsbauer eine Art Gummifarbe (SC 2000 und SC 4000), die zur Reparatur und Neubeschichtung von Industrieförderbändern genutzt wird. Ich habe auch eine Weile auf spezielle Yachtlacke auf PU-Basis spekuliert. Letztendlich habe mich mich gegen das Selbstbeschichten entschieden, da ich keine Hinweise auf die Lebensdauer solcher Häute habe finden können. In früheren Zeiten haben Selbstbauer wohl auch Gummi von Auto- und Fahrradschläuchen mit Hilfe von Benzin aufgelöst und dieses Flüssigkeit zur Beschichtung verwendet.
Teichfolie aus PVC oder einem ähnlichen ökologisch verträglicherem Material schied von vornherein aus - Teichfolie besitzt kein Trägergewebe. Zwar ist diese Art Folie sehr elastisch und widersteht sehr hohem Druck, aber sie ist recht empfindlich gegenüber mechanischer Beschädigung. Letztendlich habe ich mich für LKW-Plane vom Autosattler entschieden. Sie ist als Meterware in jedem größeren Ort zu bekommen, läßt sich leicht zuschneiden, ist preiswert und es gibt sie in vielen verschiedenen Farben und Stärken. Zudem hatte ich im Internet viele Hinweise auf die Möglichkeit gefunden, PVC-Plane zu kleben und zu schweißen. Aber ich bis es soweit war sollte ich noch viel Lehrgeld zahlen...
LKW-Plane läßt sich eigentlich ganz gut mit einer Haushaltsnähmaschine vernähen. Meine Singer stammt aus den 30er Jahren und ist mit einem japanischen Elektromotor bestückt. Kompliziertere Nähte vor allem im Bereich von Bug und Heck habe ich mit einer Nähahle von Hand genäht. Die Löcher für die Nähte brauchten nicht vorgebort zu werden.
Das Obermaterial klassischer Faltboote besteht zumeist aus dichtgewebter schwerer Baumwolle. Mitlerweile gehen jedoch immer mehr Hersteller dazu über, Kunstfasergewebe zu verwenden: Kunstfaser verrottet nicht, ist lichtecht und bei gleicher Reißfestigkeit leichter. Baumwolle soll für das Innenklima des Bootes angenehmer sein, darf aber nicht feucht verpackt werden, um Stockflecken zu verhindern. Ich habe mich für einen Markiesenstoff aus Polyestergewebe entschieden, weil dieser recht leicht ist und auch sehr wasserfest. Zudem bleibt der textile Charakter des Bootsdecks erhalten. Andere Bootsbauer scheuen sich nicht, für das Oberdeck ebenfalls PVC-Plane zu verwenden. Es handelt sich letztendlich also um eine reine Geschmacksfrage. Als Verstärkung für den Bug und das Heck sowie für Abspannpunkte der Lebensleine und der D-Ringe, an denen auf Deck geschnallte Ausrüstung befestigt werden kann, habe ich Cordura verwendet. Genäht habe ich mit handelsüblichem Polyestergarn, alle Nähte sind in 3- und 4-fach genäht.
Alle Fotos 
Weiter zu Seite 6
Home
zurück
|
|